Vacuum hardening
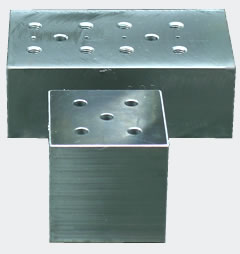
Vacuum hardening
Deep hardening under vacuum atmosphere
Austenitising temperatures up to max. 1400°C
Quenching in nitrogen overcompression
- Bright surfaces
- Very good reproducibility
- Distortion-resistant through mild quenching medium
Vacuum hardening in performed in state-of-the-art process control computer facilities in our company.
Capacity, sizes
Components/workpieces with dimensions of up to max. Rd. 600x600
Batch documentation/thermal treatment diagrams.
Application fields:
Especially suited for moulds and tools made of hot and cold-work steel (e.g. 1.2379, 1.2343,1.3343…)
Drawing
Drawing is a form of annealing used to increase the toughness of a hardened component to an extent that ensures ductility which occurs due to strain. The resulting loss of hardness is accepted and also serves to set the nominal hardness required by the customer.
Several drawing treatments may be required to achieve optimum mechanical properties.
A special drawing treatment is the so-called drawing in secondary hardness maximum, which allows subsequent surface treatment of suitable materials (e.g. plasma nitriding or TIN coating) at higher temperatures without loss of hardness.
We perform drawing under shield gas, vacuum or air atmosphere.
All drawing facilities are programme-controlled. Time-temperature diagrams can be generated.
Annealing
Annealing is a generic term for a large number of different annealing methods. Annealing is used to set specific mechanical or physical properties in the material. In general, an annealing process does not increase the strength of the material. The essential annealing methods are:
Normalizing
Normalizing is mainly used on cast, hot-formed or welded workpieces in order to remedy irregular and coarse-grained weld structures, which leads to better mechanical properties. Normalizing is performed at 850 - 950°C and can be repeated several times if necessary (cyclic annealing).
This results in a fine-grained weld structure with more or less fine ribbon perlite.
Stress relief annealing
Workpieces made of ferrite materials may show internal stress caused by various methods (e.g. welding, cold forming, machining) in macroscopic or microscopic ranges, which almost reach the material's yield point.
As a result, the dimensions and shape of a workpiece may change or microscopic and macroscopic cracks may occur that may lead to breaking. This internal stress may result in excess distortion especially in later thermal treatment. For this reason, affected parts should always be stress relief annealed at temperatures between 500 - 650°C after initial machining.
Soft annealing
Steel materials with medium to high carbon contents are soft annealed for further processing to facilitate this. Spheroidizing is a special form of soft annealing. In order to prevent undesired surface effects, all annealing methods can be performed under shield gas or vacuum.
All annealing work is performed on state-of-the-art systems.