Case hardening
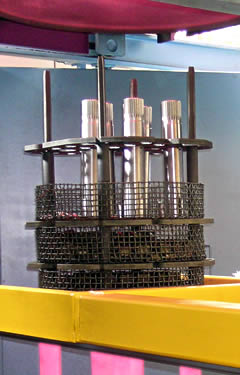
Case hardening by carburizing means case hardening after prior enrichment of the case with carbon (carburizing) under shield gas atmosphere for materials whose alloy composition would not allow martensite formation without carbon enrichment.
Einsatzhärten ist das Randschichthärten nach vorherigem Anreichern der Randschicht mit Kohlenstoff (Aufkohlen) unter Schutzgasatmosphäre für Werkstoffe deren Legierungszusammensetzung eine Martensitbildung ohne Anreicherung mit Kohlenstoff nicht zulassen würden.
Case hardening by carburizing
- Carburizing depth up to max. 2 mm
- Austenitising temperatures up to max. 1000°C
- Oil quenching
- Bright surfaces
- Positive mechanical properties through hardness gradients from the core to the case
- Very good reproducibility
- Very good flexibility through high degree of automation
We perform case hardening by carburizing in process computer-controlled, fully automatic thermal treatment tracks with batching robots. The high degree of automation ensures permanent reproducibility at the highest quality.
Capacity, sizes
Components/workpieces with dimensions up to Rd. 500x700. Individual parts as well as series with medium to high batch sizes.
Application fields:
Low-carbon materials like e.g. 16MnCr5 and 21MnCr5 (case-hardened steels).
Nitrocarburizing
Nitrocarburizing means case hardening after prior enrichment of the case with carbon and nitrogen under shield gas atmosphere for materials whose alloy composition would not allow martensite formation without carbon enrichment. Adding nitrogen at the same time also results in high degrees of case hardness with non-alloy materials.
- Bright surfaces
- Positive mechanical properties through hardness gradients from the core to the case
- Very good reproducibility
- Very good flexibility through high degree of automation
We perform nitrocarburizing in process computer-controlled, fully automatic thermal treatment tracks with batching robots. The high degree of automation ensures permanent reproducibility at the highest quality.
Capacity, sizes:
Components/workpieces with dimensions up to Rd. 500x700. Individual parts as well as series with medium to high batch sizes.
Application fields:
Low-carbon, non-alloy materials like e.g. ST2; C15
Shield gas hardening
Shield gas hardening is the deep hardening under shield gas atmosphere (hardening under neutral gas atmosphere, therefore no scaling of the component surfaces)
- Austenitising temperatures up to max. 1000°C
- Oil quenching
- Bright surfaces
- Very good reproducibility
- Very good flexibility through high degree of automation
We perform shield gas hardening in process computer-controlled, fully automatic thermal treatment tracks with batching robots. The high degree of automation ensures permanent reproducibility at the highest quality.
Capacity, sizes:
Components/workpieces with dimensions up to Rd. 500x700. Individual parts as well as series with medium to high batch sizes.
Application fields:
Materials like e.g. 115CrV3; 90MnCrV8, 100Cr6.
Carburizing
Enrichment of the case with carbon (carburizing) under shield gas atmosphere for materials whose alloy composition would not allow martensite formation without carburizing.
Carburizing without subsequent hardening may enable partial hardening. In those parts of the component that are to remain soft, the carburized case layer may be removed mechanically. This section then remains soft with subsequent hardening (strength depends on the material composition).
- Carburizing depth up to max. 2 mm
- Oil quenching
- Dimensions Rd. 500x700
- Batch documentation
- Bright surfaces
- Positive mechanical properties through hardness gradients from the core to the case
- Very good reproducibility
- Very good flexibility through high degree of automation